Double sided punching axial flux stator technology
PressAccording to the general production process of the Axial fulx motor stator, stamping and winding are carried out integrally. Each time one tooth is punched, the servo system drives the coil stock to move. However, if there are teeth on two planes of the stator, how should it be handled? There are two situations:
1. The two teeth of the stator are in parallel positions: Only need to design another punch when designing the mold, and the two teeth can be stamped synchronously;
2. The two teeth of the stator are misaligned: Since the distance between the two teeth increases as the winding radius becomes larger, the traditional mold can no longer meet the requirements; a dynamic stamping die must be designed, that is, the punch is in a moving state, and the stamping time and cycle are precisely controlled by a computer to achieve the required stamping result;
Best has been focusing on the production and process R & D of Axial fulx motor stators for many years, and has complete production and manufacturing experience for Axial fulx motor stators, including stamping, drilling, end – face grinding, annealing, and winding;
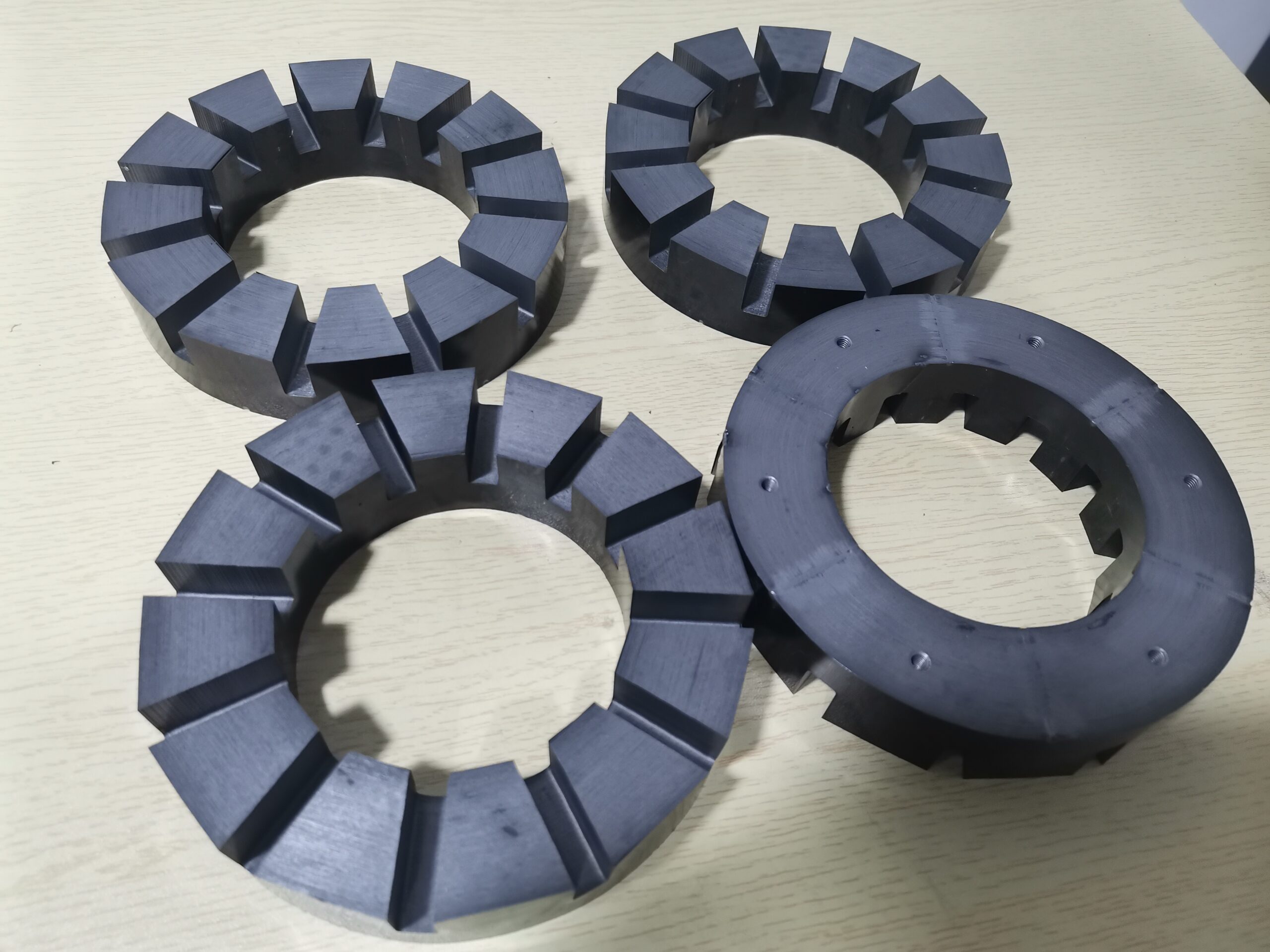
Generally speaking, except for wire cutting, which cools the product with coolant in real – time and thus has relatively small internal thermal stress, all other processing technologies, such as laser cutting and punch stamping, will generate a certain amount of stress on the sheared cross – section. This stress will disrupt the internal magnetic field distribution of the silicon steel sheet, resulting in an increase in losses. The thermal stress annealing process is a special treatment process carried out to improve the performance of the product after stamping.
Axial flux stators are generally produced by special equipment through stamping and winding. Therefore, it is inevitable that a certain amount of punching and shearing stress will be generated at the stamping part during the stamping process, which increases the eddy current of the motor. Therefore, for high – performance axial flux stators, we recommend annealing heat treatment to eliminate the internal stress of the axial flux stator and improve its performance.
Baist has many years of experience in the production of rotors, stators, and motors. It can perform targeted annealing treatment according to the material characteristics of different silicon steel sheets.
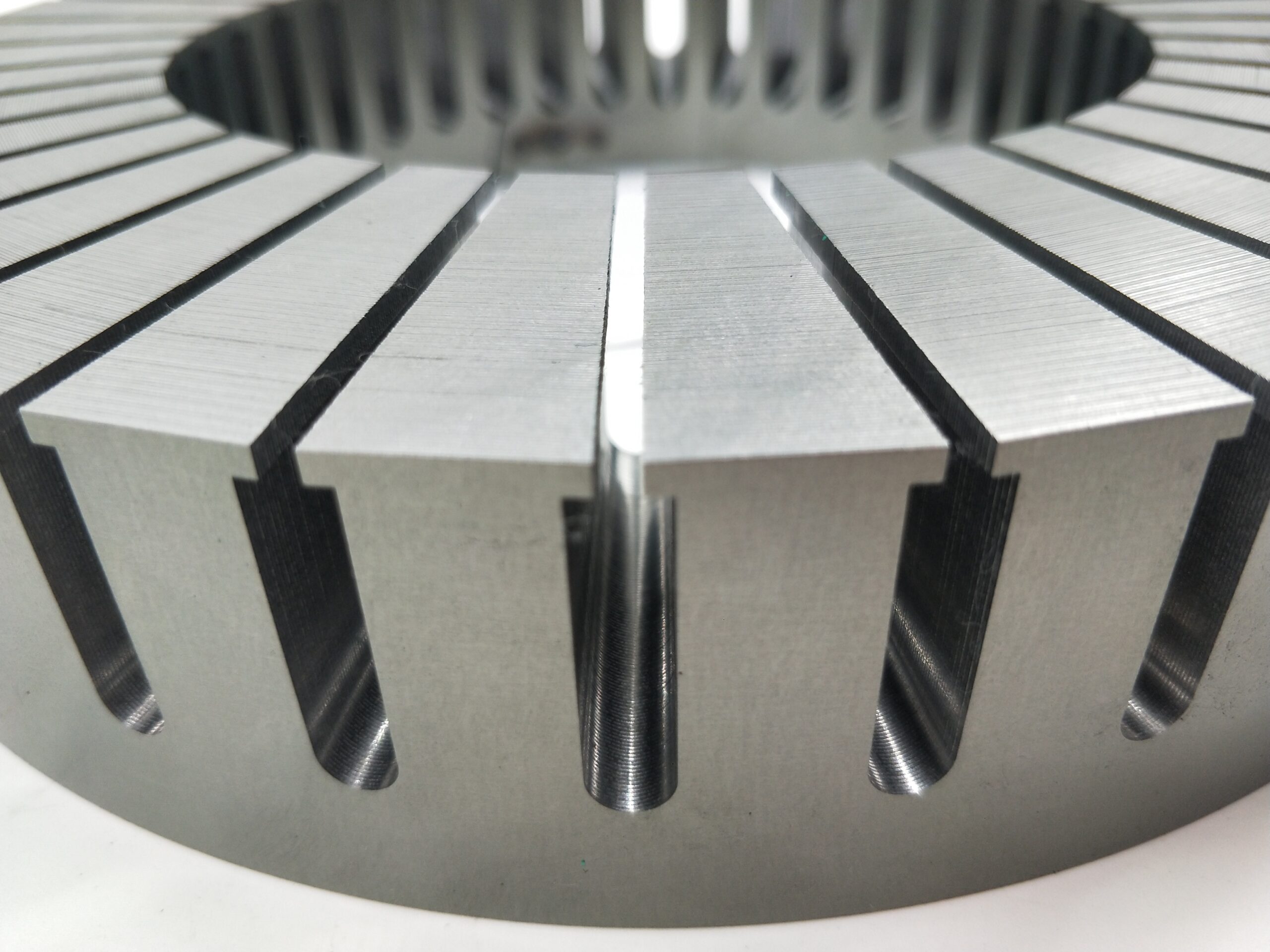
Stamping and winding process for Axial flux motor sator
Axial flux motor sator is currently replacing traditional motors in more and more fields due to its compact structure and high motor power density, and has achieved very good results;
The production of Axial flux motor sator is essentially different from the traditional stator core. The traditional stator lamination direction is to press or cut a single piece of the same shape, adopt a suitable lamination process, and stack axially to achieve the parameters and height required for product design; The Axial flux motor sator adopts a dedicated stamping and winding integrated equipment, which uses a dedicated stamping die to punch the groove shape and a servo synchronous control system to accurately control the stamping frequency and winding speed, in order to achieve consistent alignment of the product from inner diameter to outer diameter;
Best has been focusing on the development of Axial flux motor sator technology for many years. After years of research and development investment, it currently has 6 independently designed and developed disc stator stamping and winding systems, which can meet the daily production capacity of 1000pcs; Due to the machine being completely independently designed and developed, we can increase production capacity by 3-5 times within 2 months;
Best provides one-stop Axial flux motor sator solutions from raw material procurement, product stamping, winding, drilling, gluing, welding, annealing, and winding. Currently, we have formed strategic partnerships with several well-known German, British, and Swiss disc motor brands to provide them with comprehensive axial flux stator solutions (AVID, Borggarner, etc.);
The production process of the Axial flux motor stator is stamping + winding. Through the control of a precision system, these two processes are carried out synchronously. The number of teeth and the lamination thickness are both determined by the settings of the operating system; In fact, when winding, since the tooth material of the Axial flux motor stator product has been stamped and sheared off, it cannot be wound in a theoretical circular shape, but will become a polygon. The side length of the polygon is directly related to the size of the stator and the number of teeth; When the outer diameter of the stator is relatively large (over 200mm) or the number of its teeth is less than 24, this polygon will be more obvious;
Best can correct the polygon arc of the Axial flux motor stator through a unique technical solution, so that the outer diameters of all stators approach the theoretical arc shape; The following picture shows the difference in results when the stator is subjected to polygon correction and when it is not.