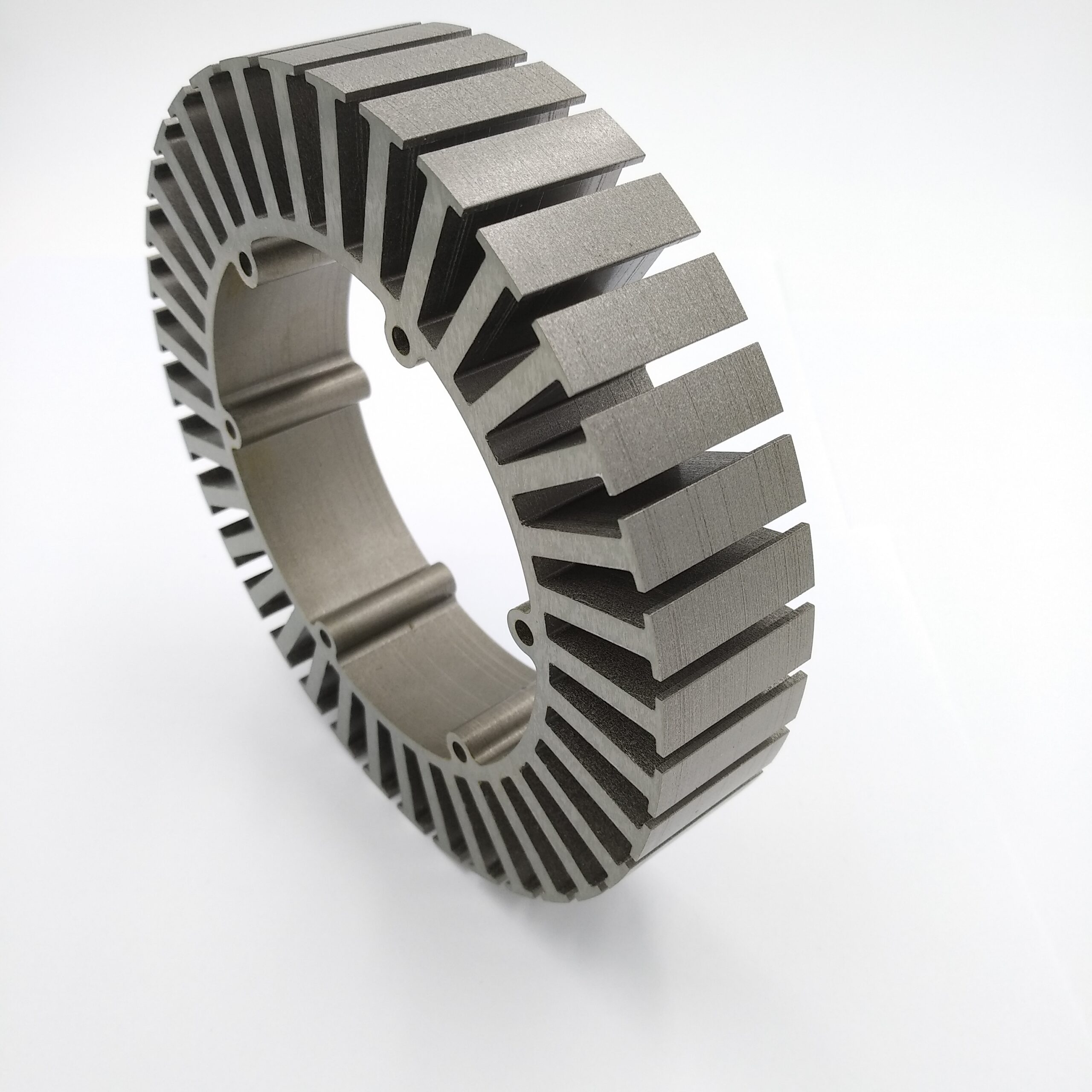
Our technological advantages:
1. Through relevant tests, a lamination coefficient of 96 – 98% can be achieved (based on 0.2mm silicon steel sheets);
2. Imported glue with UL certification that can withstand a high temperature of 200 degrees is used to ensure the safety of its electrical performance.
3. In theory, any additional loss can be avoided. After adopting other suitable processes, it can be ensured that the iron loss of the entire iron – core product meets the relevant parameters in the material specification sheet (there are relevant test reports).
4. Since glue is used for fixing between layers, the noise of the motor at high speed has been significantly reduced compared with that using the welding process.
5. Since the relevant glue forms a protective film on the product surface, it has a certain improvement effect on the anti – rust oil of the product.
6. For a general new – energy vehicle stator product with an outer diameter of 200mm and a height of 150mm, our company has a daily production capacity of 100 sets of products, and the production capacity can be increased by 5 times within 1 month according to the order requirements.
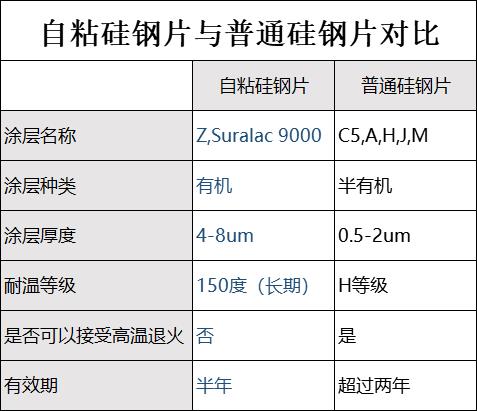
Self adhesive silicon steel sheet stator
The manual adhesive solution requires complex manual operations and complex stacking fixtures, resulting in low production efficiency and a certain scrap rate. With the development of technology, multiple steel mills have introduced self-adhesive silicon steel sheets in recent years;
Self adhesive silicon steel sheet refers to a layer of organic coating applied by the silicon steel sheet manufacturer on the surface of the silicon steel sheet after cold rolling (such as Baosteel’s Z-coating and Suralac 9000 from Sura Cogent). This coating has both the insulation properties of C5 coating and the adhesive properties of glue; After the production of silicon steel sheets, the self-adhesive coating is non adhesive (B state). When the product is under certain temperature and pressure conditions, the self-adhesive coating will melt and form a curing strength to bond the silicon steel sheets together, achieving the bonding effect; The relevant parameters of self-adhesive silicon steel sheets compared to ordinary silicon steel sheets are shown in the figure:
Through years of experience accumulation, Best has continuously developed self-adhesive silicon steel sheets and self-adhesive iron core processes. Currently, the self-adhesive iron cores produced far exceed peers in terms of tolerance size control, appearance, and adhesive strength; And it has received praise from many European and American customers such as Germany, Switzerland, and the United Kingdom; At present, Bestech has a stock of self-adhesive silicon steel sheets of 0.2mm, 0.25mm, 0.35mm, and 0.5mm to meet the different customized iron core needs of various customers