Introduction to various types of stampin
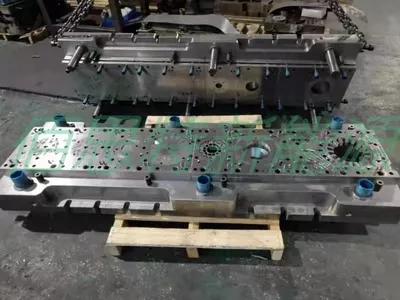
Progressive continuous mode
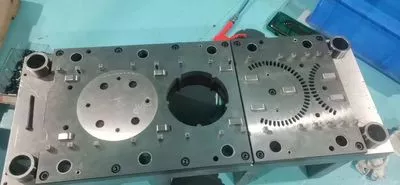
Composite stamping die
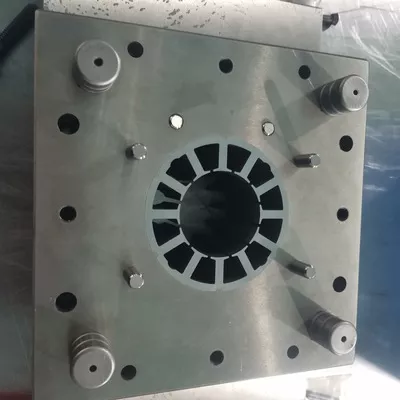
Single punch die
Mold Introduction1
Single punch mold
A single punch mold, also known as a soft mold, is generally composed of one concave mold and one convex mold or multiple concave dies and multiple convex molds. During the punching process of a punch press, only one punching process can be completed in one row. Therefore, when designing a fixed rotor sleeve punching, it is necessary to design separate single mold to achieve this;
The advantages of a single mold are as follows:
1. The structure is simple and the mold cost is relatively low. Generally, the cost of a single mold varies from thousands to tens of thousands of yuan depending on the size and design of the product;
2. The single mold cycle is relatively short, usually taking 3-4 weeks to complete. In case of urgent orders, it can be completed within 2 weeks;
3.Due to its simple design, there is a high degree of redundancy in product design changes. After the design change, the cycle and cost of remaking a new mold are much lower than those of progressive molds; Especially in the early stages of product development,
4.Compared to wire cutting samples, its product unit price is lower, but it can achieve the same dimensional accuracy as fast wire cutting;
The restrictive conditions for a single mold are as follows:
1. Due to the one-time stamping process, it is difficult to control product deformation, and the ellipticity of single silicon steel sheets after stamping is generally poor
2. The structural design of a single die is simple and cannot achieve automatic continuous stamping. It requires manual feeding and taking, and the cost of single die stamping is relatively high
3. Due to its design concept of completing product validation work before mass production, the design life of a single mold is generally within 100000 strokes, and the value of upgrading to improve its life is not significant;
4. Due to the use of general grinding tool steel as the material for the mold, burrs are easily formed on a single piece after stamping, and it is difficult to fundamentally solve the problem;
5. Single punch mold generally use low-speed Cshaped punch presses, and because they require manual operation, their production efficiency is relatively low; Generally, only 5-10 iron core pieces are produced per minute;
Composite mold
The single mold structure is simple and cost-effective, but it cannot punch complex shaped products, especially when designing the inner rotor of the motor, and when the rotor is also designed with silicon steel sheets inserted into magnets or surface mounted magnets, two sets of single dies need to be opened to complete the stamping of the fixed rotor, resulting in increased mold costs and material waste; Therefore, composite molds have significant advantages in small batch stamping of complex shaped rotors and stators
The advantages of composite molds are as follows:
1. Compared to progressive molds, it uses ordinary mold rigidity and simplified structural design, resulting in significantly lower costs than progressive molds
2. Because he adopts a step-by-step design concept, the size and deformation of the stamped single piece are better than those of a single die;
3. Its steps are generally only 2-3 steps to reduce production and manufacturing costs;
4.If maintained properly and using high-quality mold steel, the mold life can reach millions of impacts
5. It is possible to achieve fixed rotor sleeve punching to improve material utilization and reduce product unit price
The limiting conditions for composite molds are as follows:
1. Its stamping speed is similar to that of a stamping die, only 30-60 times per minute, resulting in lower production efficiency;
2. Its tolerance and product roundness cannot reach the tolerance level of progressive dies
3. Due to the use of ordinary mold steel, regular maintenance is required to prevent severe burrs;